アルミ等温押出
RcdWin
RCDIGITAL,Inc.
November 2022>
1
アルミ等温押出
等温押出プログラムの特徴
- パラメータの調整で+-1℃の誤差で等温制御が可能です。
- 等速押出で実績のある立上係数により、等温立上げの自動調整が可能です。
- ビレット温度(ビレットテーパー温度)の自動調整
- 上限押出速度を監視しているので、押出速度の暴走の危険がありません。
-
押出管理プログラム(EM)による等温押出パラメータのデータベース化。
-
押出管理プログラム(EM)による、放射率の自動調整。
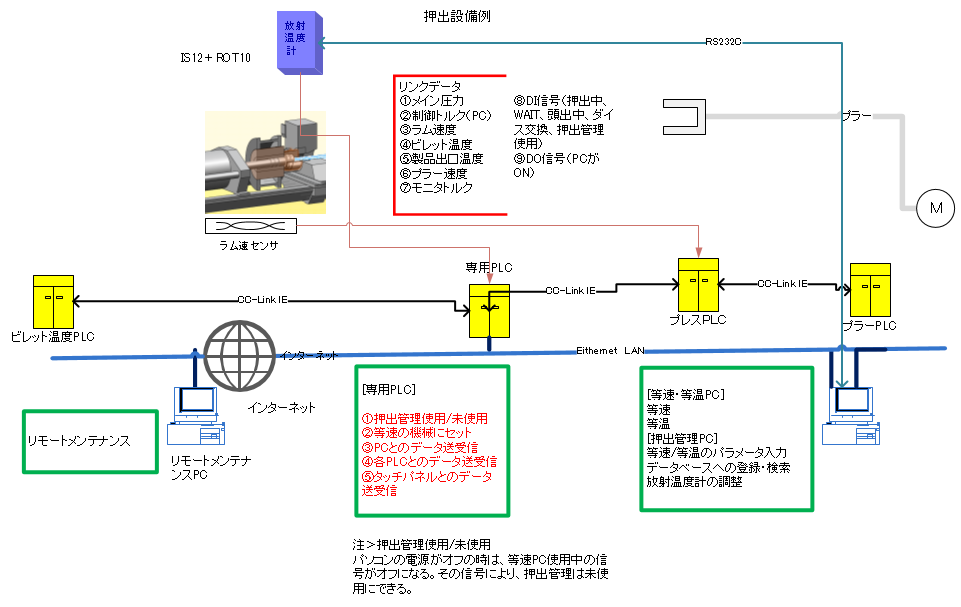
図番1-1 等温押出システム図
↑TOP of Page
2
等温押出の事例
2-1
等温押出ONとOFFの比較
1 生産性の向上
等温押出は、立ち上げ時にオーバーシュートさせるので、等速押出より立ち上げが早くなります。
図番の2では、等温押出をするために、ラム速度が最初から最後まで傾斜しています。しかし、ビレットテーパーやQRコンテナなどで温度制御を行えば、ラム速度が傾斜しないで等速に近づきます。設備の等温押出対応で、生産性がさらに上がります。
2 品質の向上
等速押出はアルミ形材表面のアルミ成分の均質化、等温押出は、アルミ型材内部のアルミ成分の均質化があるといわれています。
パラメータの調整で、+-1℃の誤差等温押出も可能です。
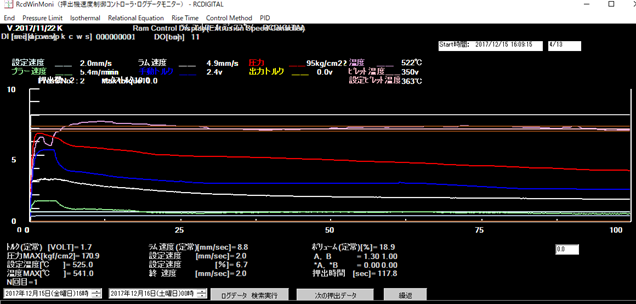
図番2-1-1 等温押出 温度の誤差は+-5℃の設定です。設定温度525℃、ビレット温度は、450℃。
温度の誤差を+-1℃に設定すれば、製品温度はさらに直線になります。
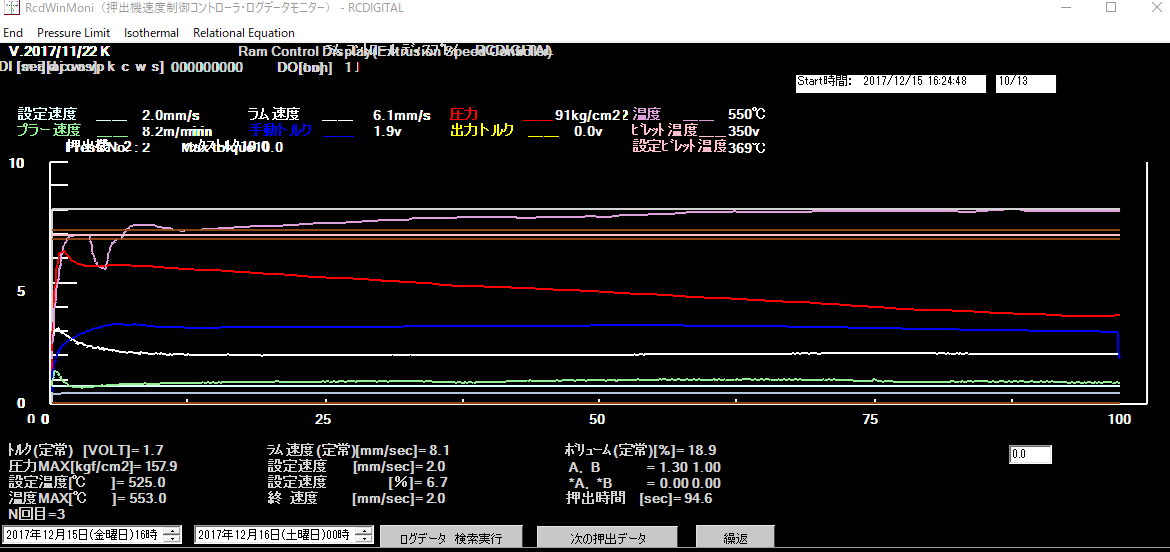
図番2-1-2 等温押出をOFFにした時。ピンクの製品温度が上昇しています。
↑TOP of Page
2-2
傾斜押出としての等温押出
傾斜押しでは、アルミ形材の温度の上昇防ぐために、コンピュータに設定したパラメータにより設定速度を滑らかに傾斜させました。ラム速度は、その設定速度の傾斜に追随します。
アルミ形材の温度を放射温度計で測れるようになりました。そのため、コンピュータに予め設定した傾斜のパラメータではなく、直接形材の温度を監視しながら、形材の温度上昇を防止できるようになりました。
等温押出の FIG12-1、FIG12-2 を見ると、傾斜押しと同じような設定速度のパターンになっています。傾斜押しと異なる設定速度のパターンを示すのは、温度に余裕がある場合です。この場合、FIG12-3,FIG12-4のように設定速度が傾斜するのではなく上昇しています。
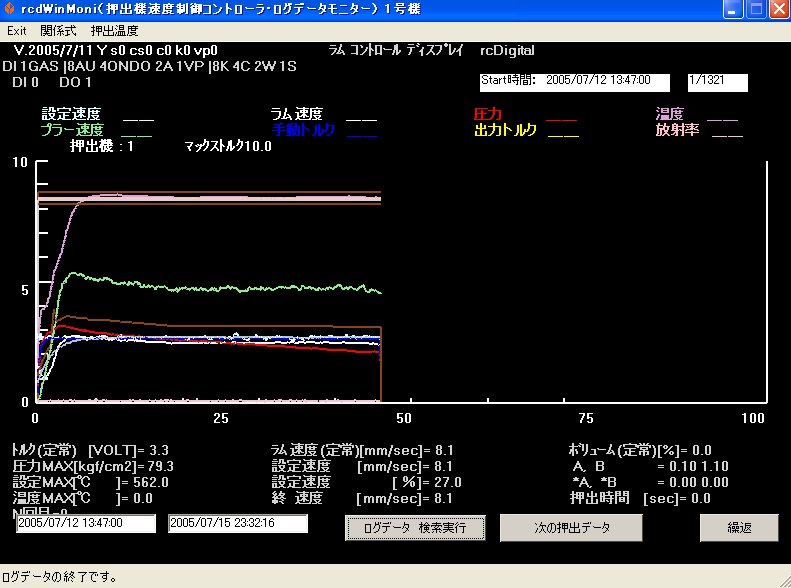
図2-2-1 製品温度上昇防止のため、速度が傾斜しています
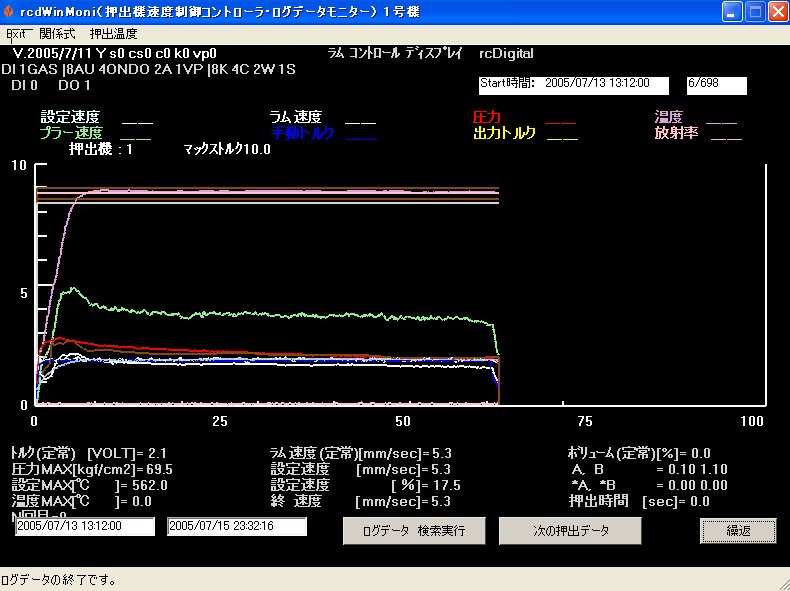
図2-2 -2製品温度上昇防止のため、速度が傾斜しています
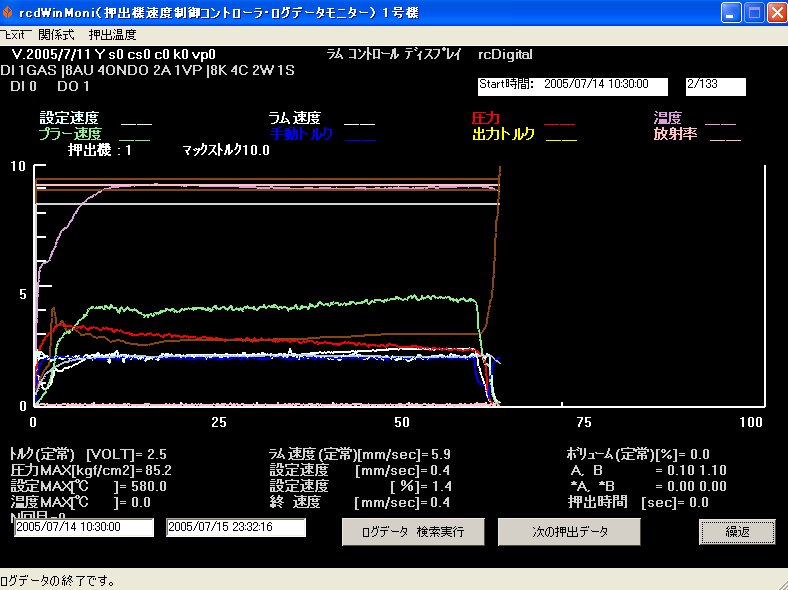
図2-2-3 製品温度に余裕があるため、速度が上昇しています
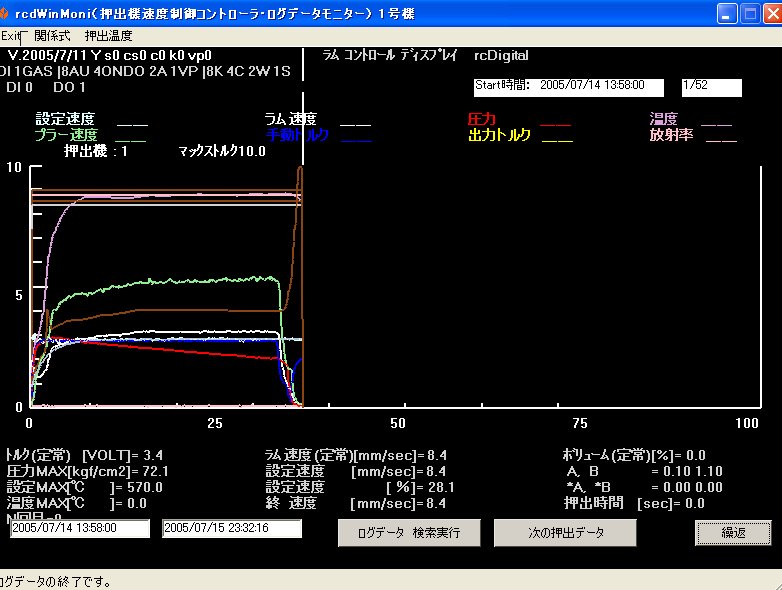
図2-2-4 製品温度に余裕があるため、速度が上昇しています
注>図のピンクの線が温度です。
↑TOP of Page
2-3
生産量の増加と等温押出
アルミの押出で生産量を上げるためには、ラム速度の立ち上がり時間を短くし、設定速度を高くします。
ただし、設定速度を上げると製品の品質不良発生の要因になるので、どれだけ設定速度を上げることができるかは難しい問題です。
品質不良発生の原因として製品の温度上昇があります。等温押出では、押出が定常後の製品温度の上昇を防止できます。そのため、定常後の温度の上昇分⊿Tを、設定速度⊿Vに換算します。そして、⊿Vを設定速度の上昇分とします。これにより、温度上昇に起因する品質不良発生を防止し、尚且つ生産量を増加させることができます。なぜなら、新たな⊿Tの温度上昇は等温押出で防止できるからです。
設定温度は押出が設定速度に到達し、定常状態になった時の温度にします。 これにより、設定速度が与えられれば、設定温度は自動的にコンピュータにより押出制御中に求まるので、設定温度の指定の必要がありません。
しかし、アルミ押出工場の要求は、設定温度を指定して、早くを製品温度が設定温度になるように制御するように変わりました。図13-4 等温押出例です。そのために、立ち上がりのラム速度は強制的にオーバーシュートさせます。
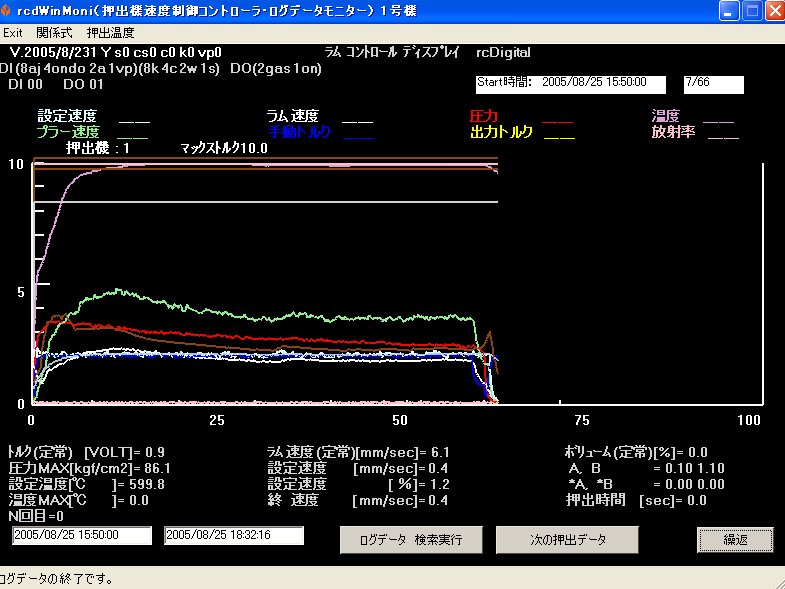
図2-3-1 等速押出に比べて設定速度を割増しています。ラムの立上がりで設定温度を自動的に求めます。等温押出で、ラム速度が傾斜しているのがわかります。
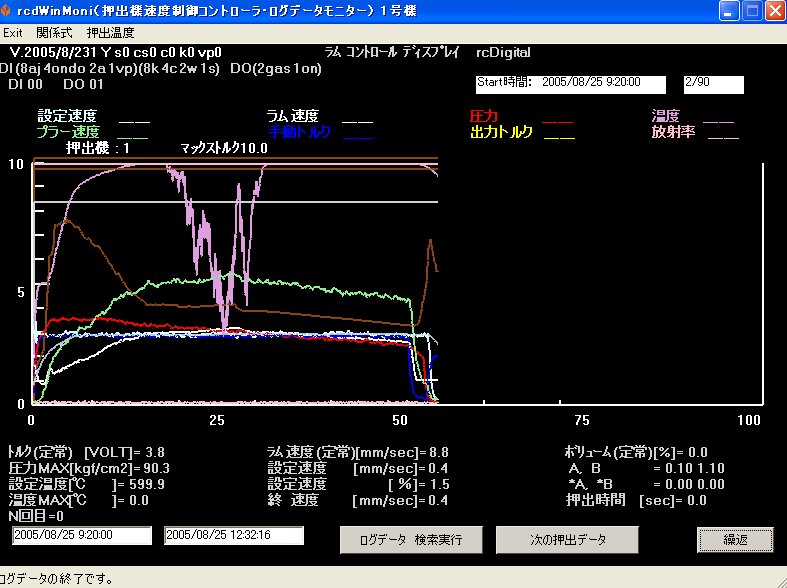
図2-3-2 押出の真ん中で製品温度が乱れています。そのため、自動的に一時等速モードに切り変わっています。製品温度が正常になると自動的に等温押出をします。
↑TOP of Page
3
等温押出パラメータ調整の自動化
等温押出のパラメータは、製品温度、ラム速度、ビレット温度の3個のパラメータがあるので、調整が難しいです。
等速押出ではラム速度だけです。
しかし、手動の等温押出に比べて多くの点を自動化しました。
-
製品温度が設定製品温度になるまでの立ち上がりは、等速押出で効果のあった立上時間と立上係数で自動化しました。
-
立上がり係数でうまくいかない場合は、ビレット温度を自動調整するようにしました。
-
製品温度が設定温度に到達した後は、自動的に温度を一定にします。
-
等温状態でも、ラム速度やビレット温度が異常な場合は不良になります。図番3-1参照。デフォルトで設定押出速度のプラスマイナス10%以内で、等温制御を行います。
- 放射温度計は、通常、押出ダイスごとに正しい温度を計測しているかどうか調整する必要があります。製品温度を取得するために、放射率の調整が必要なタイプの放射温度計に対しては、放射率の調整を自動化しました。
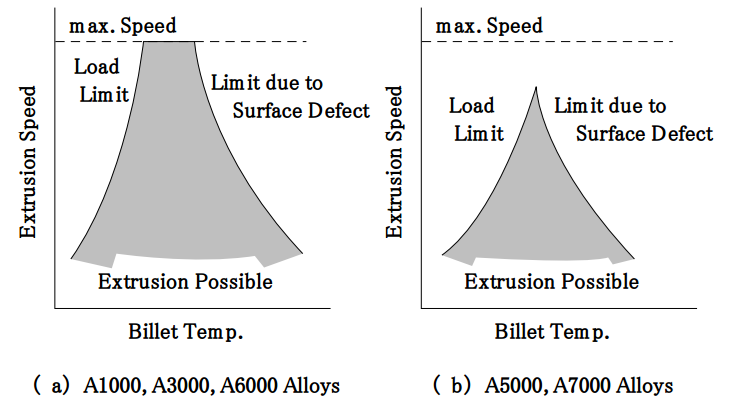
図3-1 押出速度やビレット温度が高くなるほど、製品の良品の割合が小さくなります。材質により、その割合は異なります。(アルミニウム合金の押出し限界線図)。
↑TOP of Page
4
等温押出プログラムのパラメータ入力画面
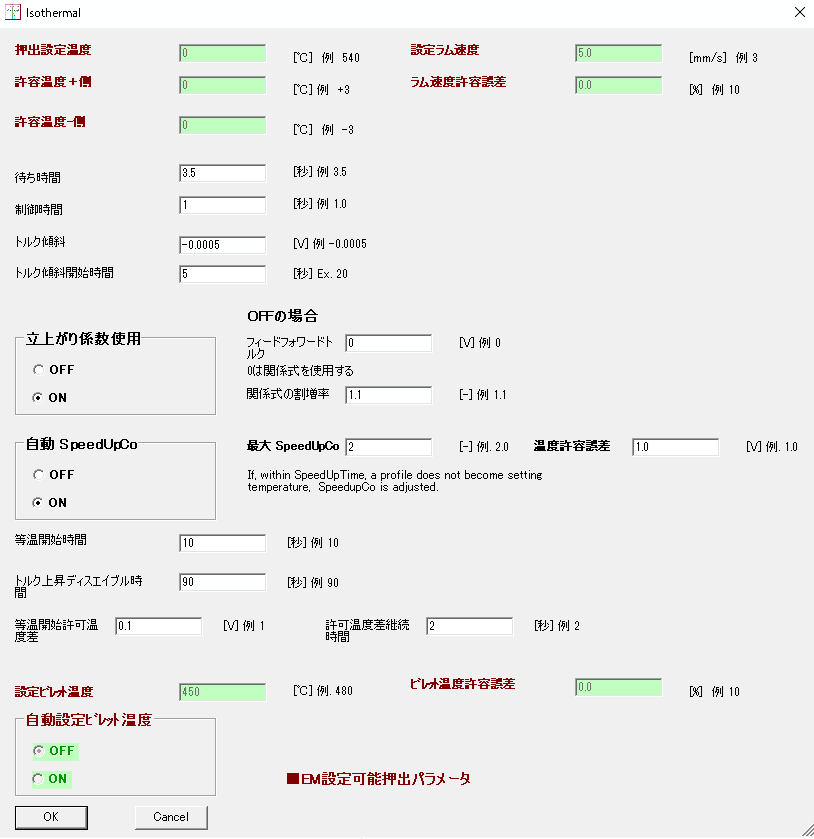
図4-1 等温押出プログラムのパラメータ入力画面
緑の入力ボックスは、押出管理プログラム(EM)で入力します。
↑TOP of Page
5
押出管理プログラム(EM)
5-1
押出管理プログラム(EM)の等温押出画面
-
[機械にセット]ボタンを実行で、画面の押出パラメータが機械にセットされます。
-
[データベース登録]ボタンを実行で、データベースに押出パラメータが登録されます。
温度の設定は、[出口温度Low]と[出口温度High]で行います。
-
[自動設定ビレット温度]をONにすると、自動でビレット温度を調整します。初期値は[設定ビレット温度]です。計算したビレット温度は、緑の[自動設定ビレット温度]に表示されます。
自動設定ビレット温度は、立上り係数の自動だけでは、温度の立ち上がりが遅い場合に使用します。
-
[誤差押出速度]は、[設定押出速度]の許容誤差です。
-
[誤差ビレット温度]は、[設定ビレット温度]の許容誤差です。
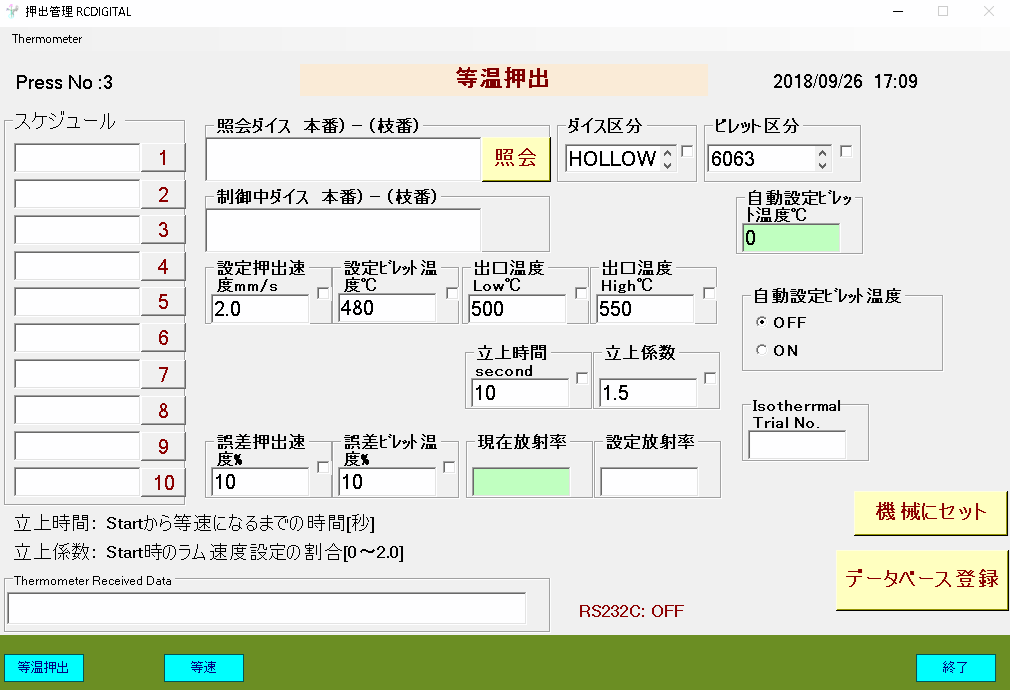
図番5-1 等温押出の押出管理
↑TOP of Page
5-2
等温押出パラメータのデータベース化
2回目以降、同じダイスを使用して等温押出する場合は、1回目の等温押出パラメータを呼び出し
て、等温押出ができます。等温押出のパラメータは調整が難しいので、生産性向上のためパラメー
タデータベース化が必要です。
↑TOP of Page
5-3
RS232Cのパラメータ設定画面
- 通信速度、ストップビット、パリティー、データ長、ポートをセットして、[Parameter Set]を実行します。
- RS232Cの通信を開始するには、[232C Stat]を実行します。
- RS232Cの通信を終了するには、[232C Stop]を実行します。
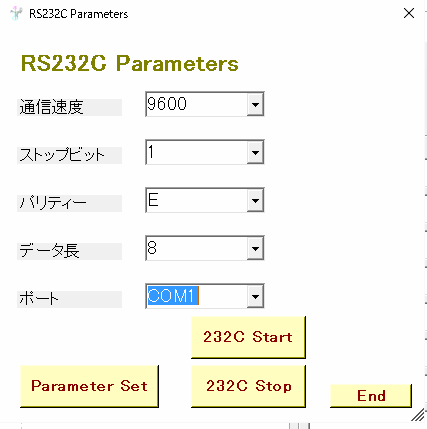
図番5-3 RS232Cのパラメータ設定画面
↑TOP of Page
5-4
放射温度計の調整
-
[Send Message]のテキストボックスに放射温度計のコマンドを入力します。
- [Send Data]でコマンドを実行します。放射温度計からの応答は、[等温制御画面]の[Thermometer Received Data]テキストボックスに表示されます。
-
通信に不具合がある場合は、[RS232C Reset]を実行します。
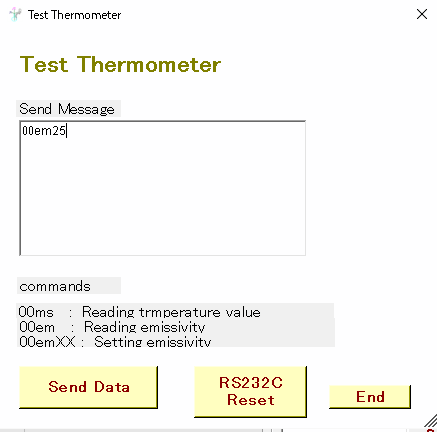
図番5-4 放射温度計の調整
↑TOP of Page
5-5
放射率の自動調整
出口製品温度を入力して、放射率を計算し、放射温度計の温度を調整します。
- [Profile Temperature]に接触温度計などで計測した温度を入力し
- [Min emissivity]に最小の放射率を入力します。
- [Max emissivity]に最大の放射率を入力します。
- [Temperature tolerance]に放射温度計の温度と[Profile Temperature]の許容誤差を入力します。
- [timer]で、放射率計算間隔を指定します。
- 温度が[Profile Temperature]まで上昇した時に、[Start Calc]を実行します。許容誤差が[Temperature tolerance]になると、計算を終了します。[Stop Calc]でも、計算を終了できます。
- 計算の履歴は[Temperature and Emissivity History]に表示されます。
- 通信に不具合がある場合は、[RS232C Reset]を実行します。
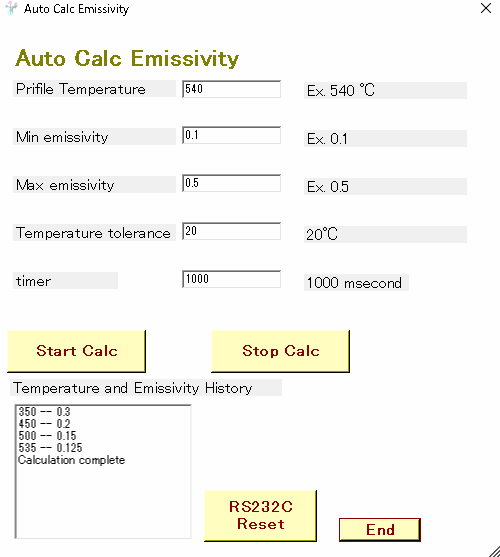
図番5-5 放射率の自動調整
↑TOP of Page